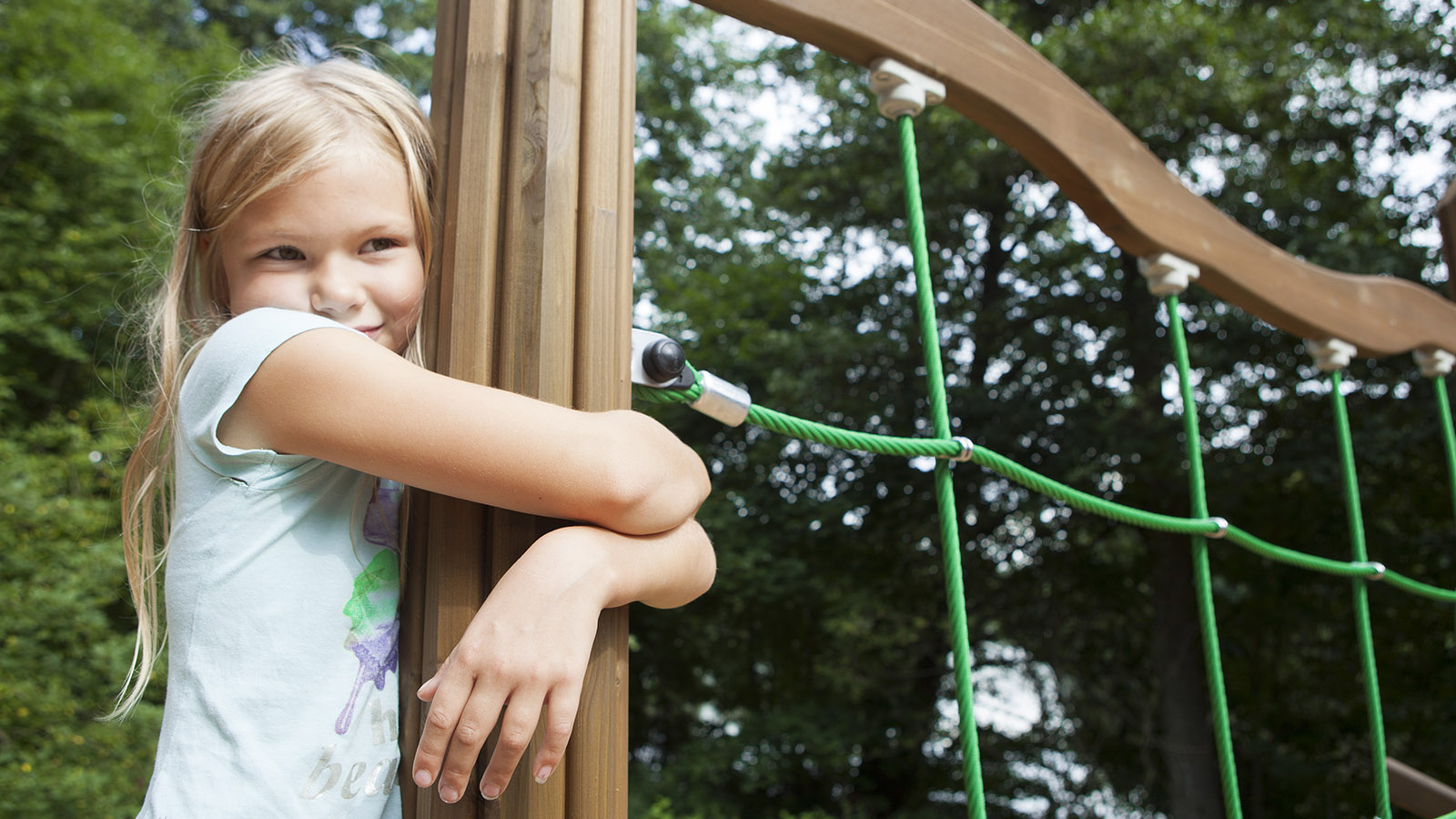
Sustainable development by making wise choices
At Lappset Group, we understand that sustainability starts from design and material choices. We use electricity from renewable sources to power our operations, creating equipment that provides movement opportunities equally for all. We work with trusted partners who share our values of social responsibility and high-quality service. All materials in our products can be recycled at the end of their life span, and our manufacturing takes place in Rovaniemi and in Northern Europe – an effort to provide work for people in the local area. Our commitment to sustainability is essential to everything we do.